Facilities Management and New Technology Yield Significant Cost Savings
The Challenge
Change, particularly in the business arena, seldom comes easy. Facing a pending merger with another industry leader, the real estate and facilities management department of a major chemical company needed to solve a complex challenge. To help pave the way for a successful merger, the company’s senior management called for cost and staff reductions across the enterprise.
Compounding this challenge for the facilities management operation was that it wanted to preserve its loyalty to the department’s employees and maintain high service levels. Facilities management executives saw outsourcing as the solution. The goal was to eliminate staff but keep the people employed with a managed services partner that could assume responsibility for critical facilities management services and deliver them at lower costs, all while maintaining service quality.
The key was finding the right partner. The plan was to contract with a managed services provider that offered expertise in at least three critical areas:
- A top-quality human resources operation. While outsourcing would meet the need of eliminating staff, an outsourcing partner with the right HR experience could help ensure that employees would be well taken care of in terms of training, development and career advancement opportunities.
- The ability to oversee a comprehensive range of related facilities management categories in an integrated fashion. These services spanned mail, shipping and receiving, warehouse management and internal and commercial print services. Managing all of these services in an integrated way would improve operational efficiency and service quality while reducing costs.
- Experience in quality management methodologies and systems. Leveraging this expertise could help drive continuous performance improvement in the facilities management operation.
Our Solution
The sourcing firm issued a request-for-proposal and ultimately selected Canon Business Process Services as the only provider that could meet all of the desired requirements. The RFP process revealed that others competing for the business could offer expertise only in some of the targeted facilities management areas. This would prevent them from effectively integrating the functions and ultimately providing the cost savings the chemical company wanted. Only Canon had proven experience in all of the services. The chemical company had found the right partner.
Canon moved ahead, assuming management of the company’s facilities management staff (45 employees to date) and implementing changes that continue to advance the operation. One example is warehouse management, which spans the receipt, storage, inventory control and distribution of virtually everything that moves throughout the company’s main campus, including hazardous materials. Canon helped improve the efficiency of many of these activities by installing a sophisticated asset tracking and management system.
For the company’s print center operation, Canon created a state-of-the-art electronic print operation, upgraded equipment and introduced more efficient processes and solutions. The latter includes an electronic print job submission and tracking system. This enables the chemical company’s employees to use web-based portals to submit and track the status of print job requests. One system covers internal print jobs, while the other is used for commercial print services. These changes in the company’s overall print management strategy also provide more advanced chargeback capabilities and cover the company’s full range of print needs, from high-volume black and white and color printing to producing oversized documents with full finishing capabilities.
Canon went even further to achieve business benefits within the commercial print function by providing a professional print buyer. This executive uses a third-party online procurement system to purchase approximately $4 million of commercial print services annually. With the new procedure, an employee electronically submits a commercial print job request. The print buyer posts the request on the online procurement system and selects the top two or three bids. These are discussed with the employee managing the project, and final decisions are made based on price and turnaround time.
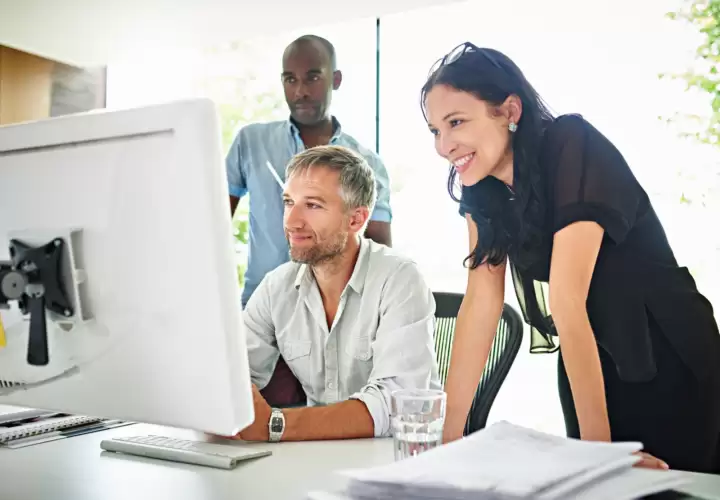
Getting Results
Canon’s new approaches are getting results. Introducing more efficient workflows, particularly in the shipping and receiving and print center location, has freed up a significant amount of office space previously devoted to facilities management activities. This space is now being used for other core business functions.
By integrating facilities management functions and implementing new technologies and approaches, Canon has helped the company save an estimated $500,000 annually. The new system for managing commercial print projects has yielded an additional $800,000 in cost reduction, bringing total savings to approximately $1.3 million to date. Canon and its client are also examining ways to ensure continuous process improvement by leveraging Canon’s quality management capabilities. This includes Canon’s expertise in Six Sigma-based® methodologies and BusinessInsights, Canon’s analytics and reporting tool designed for clients needing business performance metrics that can help them benchmark and continuously improve document-intensive processes.
With these achievements, the chemical company has not only met the demands of change posed by the merger—it is better prepared to fulfill its mission. This includes using innovative science to promote health and safety around the world. Canon’s vision is to continue helping clients like the chemical company meet such important goals, today and in the future.