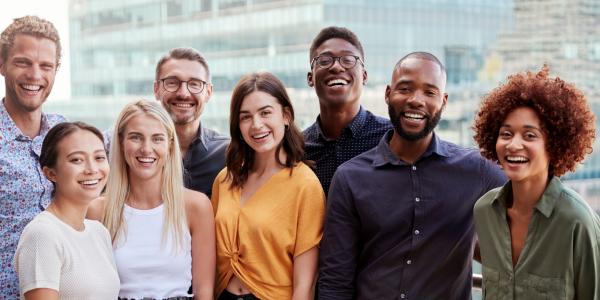
What is an inventory management system?
Find out more about Canon’s innovative warehouse management solution.
Learn moreWhat is inventory management?
Inventory management is the process of efficiently overseeing the acquisition, storage, and utilization of goods and materials within a business. The purpose of inventory management is to ensure there is enough stock at the right place and at the right time to meet customer demands. By maintaining optimal stock levels and efficient distribution, inventory management helps businesses operate smoothly and effectively.
What is an inventory management system?
An inventory management system is the system built to track, control, manage orders and optimize a company’s inventory to increase profitability. They are used to prevent inventory shortages and ensure that there is proper availability across the organization’s supply chain. Inventory management systems streamline and automate inventory-related tasks across the organization.
The importance of an inventory management system
Effective inventory management is critical to the overall stability of the supply chain. Too little available stock and the organization can’t meet their customers needs and fulfill orders, leaving money on the table. Too much stock and the product can become expired or outdated and therefore become unsellable and making the company wasteful. With an effective inventory management system, many of these headaches can be avoided. As a result, storage costs will be reduced, cash will be freed up and orders will be fulfilled on-time and without wastefulness.
Accounting for inventory
There are four different types of inventory that are tracked and managed.
Raw goods/materials: A raw good is a basic material or component that is used in the production or manufacturing of finished products. They undergo little to no processing and are the building blocks for the finalized product that is sold by the business.
Work-in-progress: A work-in-progress (WIP) good is an unfinished good that is in the process of being manufactured and transformed into a finished product. These could include goods that are currently undergoing testing or are in the process of being fully assembled.
Finished goods: A finished good is a product available for purchase by a customer.
MRO goods: Maintenance, repair, and operation supplies (MRO) goods are the items used in the day-to-day operations of the business needed for maintenance or repairs.
Inventory management methods
There are many different types of inventory management methods and techniques to efficiently control inventory levels. Each method is dependent on the businesses’ needs and the product they sell. A business can employ more than one method in their inventory management process.
- FIFO and LIFO: First-in-first-out (FIFO) refers to the sale of items that were first received in inventory. This is a common practice for inventory that is perishable or time-sensitive. Last-in-first-out (LIFO) refers to the sale of items that were most recently received in inventory. The reasoning behind this is that newer inventory has a higher cost and therefore will be less profitable.
- Just-in-time management: This method involves keeping the least amount of inventory possible to still meet customer demands before going out of stock. Inventory has to then be replenished on a continual basis. This method is useful for businesses that want to keep inventory costs low and improve cash flow. Careful coordination, planning and forecasting need to be a part of the process to use this method.
- ABC analysis: This method involves grading the value of certain stock based on how much revenue it generates for the business or how important the item is valued by the business. High-value items are prioritized in this methodology.
- Economic Order Quantity (EOQ): This is a mathematical formula that calculates the optimal quantity to order to reduce total costs including holding and setup costs. This formula takes consumer demand into account.
- Materials Requirements Planning (MRP): This system manages manufacturing processes by planning, scheduling and controlling inventory levels based on production. It measures the amount of materials needed, what is needed and how much is needed to meet all production needs for finished goods.
- Minimum Stock Level: A minimum quantity of inventory is kept in stock. When the inventory reaches a minimum threshold, a reorder is triggered to replenish stock.
What are inventory management system best practices?
- Track inventory data such as stock keeping units (SKUs), universal product codes (UPCs), stock information such as stock quantity and reorder quantity, supplier information such as contact information, storage location information for the product, returns and refunds data, purchase order data, sales data such as quantity sold, and cost and pricing information.
- Use barcode or RFID technology to assign numbers to products for tracking purposes and ensure data accuracy for picking, receiving and delivery. Detailed product information is assigned to each product.
- Maintain strong supplier relationships. Reliable suppliers are a crucial part to ensuring timely deliveries, mutually favorable pricing, and good products. In addition, if problems do arise, they can be solved more quickly and efficiently with good communications.
- Establish reordering points and lead times. Use historical sales data, forecasting and lead times to set reordering points. Use one of the inventory management methods that best coincides with your business’ and customer needs to reorder products and avoid unnecessary inventory costs.
- Regularly review inventory policies. Customer demand patterns change as do market conditions. What once worked best for your business’ inventory management operations may no longer be optimal. Make changes accordingly.
- Train employees. Staff should be trained on using the inventory management system and follow best practices. Hold staff accountable for their usage of the system to ensure data accuracy and minimize errors.
- Track inventory and stock levels. Set up routine checks for discrepancies between physical counts and system data. While inventory counts may be done annually, spot checks and cycle counts can be used to find and fix any discrepancies. With cycle counts, inventory is checked and broken down into sections and counted on rotating schedules. It can be broken down by item category, stock storage location,
- Integrate your inventory management system with other technology. Integrating the inventory management system with tools such as POS systems and mobile scanners. These systems should be synced so that the transfer of data is accurate and up-to-date.
- Outsource inventory management to an expert warehouse management outsourcing provider. When resources for inventory management, storage and fulfillment are sparse, your organization will suffer and so will your customers. Outsourcing inventory management and warehouse management will close these gaps. The right outsourcing partner can provide a holistic approach to inventory management and provide highly trained staff, proven inventory processes based on industry best practices, technology, and automation. Finding highly trained, full-time staff is a challenge for many organizations. Outsourcing solutions providers such as Canon remove the burden of managing, training and developing staff.
Perpetual inventory system
Perpetual inventory systems are providing real-time inventory tracking data through RFID tags or barcode scanning that continually update. It provides a detailed view of inventory without the need for periodic checks of physical inventory. Perpetual inventory systems are the most advanced systems for tracking inventory and are often more expensive to implement. Large organizations with high inventory turnover often benefit the most from this system as it streamlines operations and makes inventory management more efficient.
Periodic inventory system
Periodic inventory systems are systems where inventory counts are done at the end of an specific period. Beginning inventory is checked at the start of the period through a physical count of all items in stock. As purchases are made for new inventory and sales come in for when a product is sold, a physical count of all inventory is made at the end of a period. To calculate the cost of goods sold, the organization adds the cost of beginning inventory to total purchases and subtracts ending inventory. This system is typically used by smaller businesses because of their use manual and periodic counts of inventory. The system is simple and has a low cost to implement.
Key aspects of inventory control in manufacturing
- Six Sigma: Six Sigma is a data-driven technique to reduce defects and minimize variability by achieving optimal process performance. In regards to inventory management, the goal is to have just enough inventory to meet customer demand without having stockouts or excessive stock.
- Lean Manufacturing: This process has its focus on eliminating waste that doesn’t provide value to the customer. Only steps that add value to the customer are taken, allowing for a streamlined operation.
- Lean Six Sigma: This process combines Lean and Six Sigma to reduce waste, improve efficiency, enhance quality and optimize processes. Its approach focuses on eliminating defects, reducing variations and maximizing value for customers.
Tips for an efficient warehouse layout
- Analyze and optimize workflow: Understand the flow and processes of the goods within the warehouse. Create a logical flow from receiving to storage, picking, packing and shipping. Keeping the warehouse organized will enable streamlined operations and improved efficiency.
- Standardize Storage Locations: Assign fixed storage locations for specific items to simplify inventory management and reduce search time. This can be done by organizing products based on similarities or that share similar SKUs.
- Optimize space utilization: Consider the height and weight-bearing capacity of the warehouse and use this space efficiently. Optimize your floor plan for the workflow of your operations. Careful planning and design will maximize storage capacity while allowing for efficient operations.
- Create zones: Create different zones based on functionality or product characteristics. Certain areas can be designated for receiving, picking, packing and shipping.
- Keep safety top of mind: Prevent accidents and bottlenecks by clearing aisles and walkways. Keep workstations clean and organized and allow for your employees to move throughout the warehouse productively and efficiently.
- Use warehouse management systems: A warehouse management system (WMS) is a software that helps manage the operations of a warehouse. This system optimizes inventory tracking, order fulfillment, and streamlines all other aspects of warehouse management.
- Review warehouse processes: Continually review and optimize the warehouse layout by making necessary adjustments. Products, the market, and processes are often changing. It is necessary to make these changes as the supply chain changes.
Inventory management cost reduction strategies
Effective inventory cost reduction is essential for businesses seeking to enhance their bottom line. By implementing the following strategies, you can significantly cut down on unnecessary expenses:
- Implement Just-in-Time (JIT) Inventory: Embrace the JIT approach to minimize holding costs by ordering inventory only when needed. This ensures you maintain a lean inventory, reducing storage and obsolescence costs.
- Accurate Demand Forecasting: Utilize data-driven forecasting techniques to predict demand accurately. Understanding customer trends and buying patterns will help you avoid overstocking or running out of essential items.
- ABC Analysis: Categorize your inventory into A, B, and C classes based on value or demand. Concentrate on optimizing the management of high-value items (A class), as they typically contribute the most to costs and profits.
Key factors contributing to inventory cost reduction
Several critical factors influence the cost of managing inventory. By addressing these factors, businesses can achieve better cost control:
- Lead Time Reduction: Minimizing lead time helps in reducing the time between ordering and receiving goods, resulting in lower carrying costs and increased responsiveness to customer demands.
- Efficient Supply Chain Management: Collaborate closely with suppliers and maintain transparent communication to ensure a smooth supply chain flow, reducing costs associated with stockouts or delays.
- Technology and Automation: Embrace inventory management software and automation tools to streamline processes, track inventory levels in real-time, and eliminate human errors, ultimately leading to cost savings.
Inventory cost management explained
Inventory cost management involves a comprehensive approach to control and optimize inventory-related expenses. The primary components of inventory cost management are:
- Carrying Costs: These include warehousing expenses, insurance, taxes, depreciation, and interest on capital tied up in inventory. By reducing carrying costs, you can free up capital for other investments.
- Ordering Costs: These are expenses associated with placing and processing purchase orders. By optimizing order quantities and frequencies, you can minimize these costs.
- Shortage Costs: Stockouts and backorders can result in lost sales and dissatisfied customers. Balancing inventory levels with demand helps avoid these costs.
Top five proven strategies to optimize inventory
To achieve optimal inventory levels, consider implementing the following strategies:
- Safety Stock Optimization: Calculate the right amount of safety stock to maintain to prevent stockouts while minimizing excess inventory.
- Economic Order Quantity (EOQ): Determine the most cost-effective order quantity by balancing carrying costs and ordering costs.
- Vendor-Managed Inventory (VMI): Collaborate with suppliers to allow them to manage your inventory levels, reducing carrying costs and improving supply chain efficiency.
- Batch Tracking and Serial Numbers: Implement robust tracking systems to improve traceability, avoid losses, and identify slow-moving items for timely action.
- Regular Inventory Audits: Conduct periodic audits to identify discrepancies, reduce shrinkage, and maintain accurate inventory records.