Three Key Cost Savings Strategies for Your Warehouse Operation
Realize Cost Savings for Warehouse Operations
Keeping costs down is the goal of every business, which also holds true in warehouse operations. However, it’s easier said than done. The typical warehouse has so many moving parts and the demands of the current business climate are never-ending, leaving many managers with neither the time nor energy to consider new cost-cutting measures.
Labor is often the largest expense. A report from Logistics Management found that labor costs consume 50% to 70% of a warehouse operating budget. A strong economy and tight labor market only exacerbate the problem of finding reliable workers. According to a survey by Peerless Research Group, 48% of respondents said increasing wage rates to attract and retain staff is a top adjustment to operations in light of pandemic conditions, jumping 6% from last year.
Benchmark Your Warehouse Performance
Making sure that warehouse workers are not just busy, but productive. To maximize output, warehouses need to drill down to achieve a baseline metric to see who’s doing what and to cross-train workers.
Technology. The cost of installing new technology can run from thousands to hundreds of thousands of dollars, depending on the upgrade. Warehouses must decide not only how much they can afford to invest, but also the cost of not investing. Cutting back on new, even modest investments can lead to higher capital costs in the long-term.
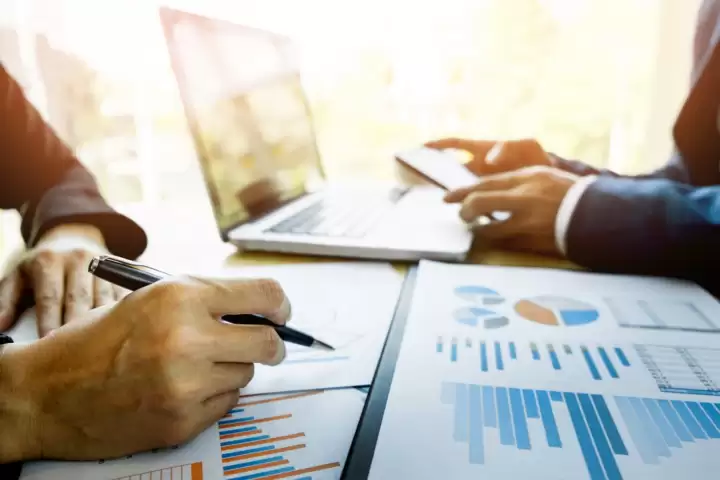
Lack of automation. Through no fault of their own, some warehouses still rely on manual paper picks to process orders instead of using a PDA or other portable digital device. To stay competitive, warehouses need to factor in automation as a cost of doing business. A study by LogisticsIQ found that the market for warehouse automation will jump from $15 billion to $30 billion by 2025.
Energy. “Warehouses in the U.S. use an average of 7.6 kilowatt-hours of electricity and 20,900 Btu of natural gas per square foot annually,” according to an announcement from Madison Gas and Electric. Warehouses can save unnecessary energy costs by installing cost-effective LED lighting or motion sensors that light up areas only when needed.
An uptick in maintaining warehouse spaces. The cost per square foot on average of warehouses jumped from $7.81 in 2020 to $7.91 in 2021, according to the Warehousing and Fulfillment 2021 Warehousing and Pricing Survey. Additionally, many warehouses don’t design their layout for greatest efficiency or shelve their items for easy retrieval.
Inventory control. According to Datex, a supply chain software and mobile computing solutions provider, the average carrying cost for warehouses is 25% of on-hand inventory value. Warehouses that don’t keep an accurate record of each item in stock risk unnecessary expenses, from maintaining overstocked items to lost sales on out-of-stock items.
Packing material. Packing products inefficiently can lead to excess costs. According to Kenco, a Tennessee-based third-party logistics company, warehouses lose money with “excessive space at the top of the trailer, crate, pallet, or individual box” with “packaging that is either considerably larger than the item or outside industry norms” and “packing material that requires a great deal of work to extricate and dispose of.”
The challenge of finding cost-effective ways to address these issues may seem daunting. However, as this paper will show, warehouses can change their operations to alleviate these pressures and make their resources go further.
Cost Savings Strategy #1: Implement More Efficient Labor Management Practices
As it is the biggest slice of a warehouse budget, managing labor efficiently can have a dramatic impact on reducing your costs. Start by collecting data on what your workers are really doing, what their level of productivity is, and what your daily goals are. You can use labor management software, spreadsheets or a basic dry erase board to track and monitor activity to help you place workers when and where you need them at a given time. “Instead of saying ‘I have 20 people, we’ll see what we get done today,’ reframe it as, ‘I have this much work that has to get done. How many people do I need to achieve that?’” says James Flora, Solutions Analyst, Canon Business Process Services.
Operations managers and HR should work together to find the right mix of full-time employees and part-time or temporary employees. Using the same temporary workers can also reduce retraining costs.
Keeping your workers engaged—productive, not just busy—can be a challenge. One solution is to break down the silos and cross-train them, allowing you to handle the highs and lows in warehouse activity strategically. “Make sure you’re effectively using the staff for all hours that they’re there on a given day, so they’re working full-time and not waiting for one aspect of the warehouse to finish before they start,” says Joe Tague, Senior Manager, Canon.
Moreover, warehouses should encourage a culture of work so that employees experiencing a lull in their activities will go to their manager and ask to be put to work elsewhere. Turning warehouse activities into friendly competitions can also drive productivity. Set realistic goals, such as the most accurate picks per hour or the longest time without creating a picking or inventory error. Some companies have found success by building incentive programs and handing out modest rewards, such as buying lunch for the crew or giving out company T-shirts.
A manager’s ability to provide accurate and timely feedback to workers is imperative. “Results oriented cultures are built by investigating and addressing issues that hinder performance as well as by publicly recognizing top employees for their contribution,” Flora says. “The latter, not surprisingly, can provide a powerful incentive to boost performance.”
Cost Savings Strategy #2: Leverage Technology to Reduce Manual Processes
Introducing technology solutions to your warehouse for the first time or upgrading your existing technology can be intimidating, depending on what you choose. However, there are some cost-effective improvements that can save you time and money overall.
In addition to the actual technology you’ll add, factor in costs associated with either finding more highly skilled workers or retraining your current workforce in the new procedures. Technology improvements don’t have to be an all-or-nothing proposition. Making changes can be done step-by-step. Tague suggests adopting a hybrid approach—finding cost-effective upgrades that deliver an immediate ROI, followed by recommendations for further technology improvements in the near future. “The measurements against productivity rates are the driving force. You wouldn’t put in tech unless it’s going to help you be more productive or do things more efficiently,” Tague says. “That’s where your ROI comes in. Your revenue is up and cost per unit is lower, which creates that very effective revenue bump.”
If you are not doing it already, a relatively simple and inexpensive solution is to equip your warehouse workers with PDAs or some other electronic portable digital device. Instead of picking and processing orders using pen and paper, they can use their electronic device to execute the transaction, saving on labor, time, and consumables. PDAs make it easier to capture inventory and productivity levels, too.
“With technology, you’re often faster, so it’s not a two-day ship time for example. Now you’re shipping the same day and keeping up with the industry. Often, technology adds a quality control component that’s going to require a scan so employees can’t pick the wrong part. These improvements can have a snowball effect by combining quality and speed to reduce costs,” Flora says.
Cost Savings Strategy #3: Use Lean Six Sigma to Drive Continuous Performance Improvement
To get the biggest gains from these and other cost savings strategies, follow the principles of Lean Six Sigma, a data-driven system of continuous improvement. Warehouses should build a working environment that values and fosters improving the efficiency of its employees on a regular basis and gets the workforce to commit to this goal. “Whether it’s improvements in technology, software or labor management, starting with a stable foundation can greatly improve the success of a project,” Flora says.
One way is to have standardized procedures for handling work and then reinforcing those procedures so that they are followed consistently and become second nature to employees. Next, focus on the ultimate goals of your operation, so that your workers understand what the customer wants, and put in place procedures that achieve that goal in the most efficient way possible. Then, track and use objective data to measure the performance of your warehouse and make any adjustments accordingly. Cost effective and high functioning work environments constantly strive to minimize the inventory in process, engage their workforce and increase the focus on quality output.
Bonus Cost Savings Strategy: Optimize the use of existing space. Regardless of the size of your warehouse or the amount of your inventory, you can slash the time and effort of fulfilling an order by using data to design the overall layout and the location of items. For example, stock your fastest-moving items closer to eye level to cut down on having to use a machine to retrieve them.
“Ensure that your high-volume picks—the items that you’re going to ship the most—are closest to your shipping or main area,” says Canon Logistics, Operations and Supply Chain Analyst Jeremy Wisdom. “Put any like items together. For example, if you’re in a retail market and you’ve got a blue shirt and blue tie that typically ship together, then locate them close together so you’re not walking across your facility to grab them. The important point is that an optimized pick path can reduce wasted movement, resulting in significantly lower costs and greater efficiency.”
Ready for The Next Step?
Cutting your costs, making the best use of your employees and resources, and cultivating a climate of improvement and engagement are key ways to prosper in today’s demanding business environment. The strategies discussed here were designed with these goals in mind—and to help ware-house and distribution centers integrate them easily, simply, and profitably. Using them to make even modest changes in the way you manage labor, capitalize on technology tools, establish continuous improvement in your corporate culture, or make better use of your warehouse space can give you a competitive edge that results in a healthier bottom-line and a stronger position in the marketplace.
There has never been a better time to adopt these best practices. To help you with these and other cost savings strategies, count on the subject matter experts at Canon. Our team of skilled and accomplished analysts will tailor solutions and improvements for you that can make a dramatic impact on the success of your operation today and in the months ahead.