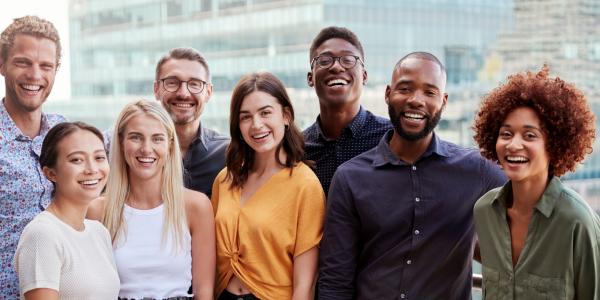
What is Warehouse Management? Processes, Performance & Solutions
Find out more about Canon’s innovative warehouse solution.
Explore Canon’s Warehouse SolutionWhat is warehouse management?
Warehouse management involves the daily oversight of all warehouse operations. A comprehensive, integrated warehouse management solution utilizes industry best practices and embraces all the essential elements that make an effective operation work. These elements span distribution and inventory management, warehousing workforce management, and business support services. Additionally, a broad range of services, provided internally or in conjunction with a services provider, might include logistics; shipping and receiving; safety processes and procedures including staff training and formalized practices that are communicated throughout the operation; environmental stewardship; warehousing and packaging; distribution and storage; quality control; technology, and equipment management.
What is the most important thing in warehouse management?
The key element in warehouse management is safety. Safety rules should span all material handling and other activities within the warehouse. These rules should be communicated as a priority to the workforce and include such principles as wearing appropriate PPE as well as paying attention to warning signs and signals. Such a secure warehouse and labor management system can help ensure consistency, efficiency, and quality control to the warehouse process, which helps improves every stage of the fulfillment process.
What are key warehouse processes?
The fundamental warehouse processes comprise receiving, putaway, inventory management, product slotting, picking, packing, kitting, and shipping. Optimizing these processes will allow you to streamline your warehouse operation, enhance product flow, reduce cost and errors, and achieve a higher perfect order rate.
The 7 essential steps to effective warehouse management
Using a retail warehouse and distribution center as an example, enhancing the following 7 steps of efficient warehouse management will help reduce operating costs, enhance supply chain management, labor management and fulfillment center processes, and optimize storage space.
- Enter the inventory. Warehouse entry is the first step in the warehouse management process. It is also the most important step for accurately managing inventory. To properly implement the warehousing process, you need to check that you receive the right product, in the right quantity, and at the right time. Not strictly following this procedure can lead to incorrect inventory, affecting the next step. Carefully monitoring this step will also help you filter out damaged products, avoiding loss and damage to the store when selling later. Warehouse management software can make it easier to maintain optimal inventory levels.
- Store. After stocking goods from a supplier, the next step in the inventory management process is warehousing. After receiving the goods, you need to arrange the goods in the warehouse using a reliable system. This helps you organize your warehouse faster, maximize warehouse space, and more easily find and pick up items when selling. Warehousing is an easily overlooked step in the warehouse management process, but it is a step that helps increase the efficiency of warehouse management.
- Picking goods. Picking is the act of collecting stock in order to fulfill a customer's order. This is the most expensive step in the warehouse management process, accounting for about 55% of total warehouse operating costs. Therefore, by optimizing your picking process, you can significantly reduce costs while increasing the efficiency of your fulfillment center. This includes limiting confusion of goods and ultimately helping to increase the customer experience. If the storage step in #2 above is done well, picking up goods should not be difficult.
- Pack and ship. Packing is the next step. It enables gathering products in each order after picking up and preparing to ship to customers. This step requires careful handling in order to limit errors and mistakes that can easily lead to refunds. Packaging regulations of each store may be different, but should meet two important goals:
- Ensure safety and minimize damage to goods during transportation
- Optimize the volume of the package to minimize delivery costs After completing the packing, you will hand it over to the shipping unit, at which time the goods will be recorded as shipped and deducted from the inventory.
- Process Returns. While no seller welcomes this step, inevitably there is a certain percentage of returned orders. Returning goods is a complex process, but there are a few principles of warehouse management when returning goods that help facilitate the process:
- Customers should follow the return policy and clearly state the cause for the return; these reasons should also be carefully documented so that adjustments can be made to reduce return rates
- There are regulations for returned goods such as re-entering the warehouse, repairing, recycling, destroying or returning to the manufacturer, etc.
- The sales and profits of the returned item also need to be deducted accordingly.
- Search for goods. Searching for goods is an activity that needs to be done regularly, not just annually or when a problem occurs. It is imperative to make sure the warehouse is always neatly arranged and that you have a reasonable inventory process in place. These factors help ensure that the inventory will take place smoothly and quickly. Warehouse management software can also make the inventory of goods much more efficient. With barcode scanners, you scan the barcode on each product to count the actual quantity in stock. After completing the inventory, you can balance the inventory so that the inventory on the software is updated according to the actual number of products.
- Leverage statistics and reports. Warehouse statistics and reports, particularly those that track key performance indicators (KPIs) can give you a view into the efficiency of your warehouse management process. There are different types of warehouse reports that you should have in order to evaluate the effectiveness of your operation as well as to create a timely and appropriate import and discharge plan. On example is an over/under-quota report, which enables you to view the items in stock that are above or below the norm, which, again enables you to craft a proper discharge/import plan.
The 5 basic principles of warehouse management
- Maintain optimal stock levels. Keeping excess stock is costly. Not being able to fulfill orders hurts profitability. The accurate and efficient receipt of stock and returns into a facility enhances warehouse and distribution center management and better prepares you for all eventualities. Warehouse management software can make it easier to optimize your stock levels at all times.
- Process sales order quickly. Swiftly and accurately processing sales orders begins in the warehouse when orders are first received and packed in your fulfillment center. Optimized warehouse management further enables fast and accurate sales order processing.
- Organize material handling and storage. Accurately maintaining stock levels and correctly fulfilling orders can only happen when you tightly control both the storage and movement of stock. It’s challenging, but the business benefits can be significant, including higher profit margins.
- Process transactions efficiently. All transactions associated with the warehouse have to be processed efficiently for supply chain management activities to work well as a whole. An efficient WMS can help you more effectively process shipping, receiving, put-aways, picking and pick face replenishments.
- Link warehouse management to sales order processing. Since warehouse management is a vital part of the supply chain, it is essential to link it to your other operational areas such as sales order processing and logistics management. This is in order to optimize how you pick, pack and ship your products out of the facility.
Benefits of an effective approach to warehouse management
There are at least 10 key benefits of an effective warehouse management system. These include:
- Optimized space
- Lower operating expenses
- Inventory visibility
- Effective labor
- Increased transparency of chain of custody
- Optimized supply chain
- Ongoing improvements via automation
- Enhanced shipment management providing better customer service
- Continuous process improvement and innovation
- Improved safety culture
To achieve these and other benefits solely through internal management is a significant challenge. For this reason, many retail and manufacturing warehouse operations choose to engage the services of a warehouse management outsourcing provider. The goal is for the provider to focus on delivering as many of these benefits as possible, while enabling the retail or manufacturing company to focus more time and resources on its core areas of expertise.
Why is a warehouse management system important?
Implementing a warehouse management system is imperative for any warehouse and distribution center operation. A WMS is important because it can yield many business benefits, which include the following two advantages:
- Lower operating costs. Effective labor management — maintaining the right staffing levels in particular — is one of the major challenges that warehouse operations face today. Having more staff within your operation than you need generally means you have higher overhead. An operational WMS system can help optimize processes, reducing the need to hire more staff.
- Inventory control and accuracy. One of the main functions of a WMS is to improve stock control and tracking. You will be able to better assist clients with the products they want by keeping current with relevant stock information. This, in the long run, should improve customer satisfaction. Better inventory control can also help remove potential operating costs incurred due to errors, which in turn can raise profits and reduce operating costs.
Who needs a warehouse management solution?
The short answer is that virtually every business with inventory that is moving through a warehouse needs a holistic warehouse management solution that spans people, process and technology. This includes businesses for which warehouse management is not a core competence as well as organizations that are expanding or not happy with the current state of their operation.
A comprehensive, integrated solution goes significantly beyond defining warehouse management as traditional shipping and receiving activities. It also enables you to more precisely track where inventory is located and helps ensure that information is up to date and accurate at all times. Effective warehouse management is one of the most important parts of conducting business in any number of industries. If a company’s warehouses are poorly run, products may be more difficult to move through the supply chain, pushing delivery dates back. As a result, profits could be impacted, and customers disgruntled, leading to other negative consequences down the line. Also, as volumes and market conditions change the ability to ramp up and down to support the business can be critical for many warehouse operations. A comprehensive warehouse management solution helps meet this goal as well.
Why use warehouse management outsourcing?
The right outsourcing partner can provide a holistic approach to warehouse services that includes focusing on four key aspects of good warehouse management: a highly trained staff, proven inventory processes based on industry best practices, technology, and automation. As an example, with its stable of safety-trained, full-time warehouse employees, Canon removes the burden of hiring, managing, training, and developing staff. By identifying a company’s key challenges, Canon can effectively leverage its own teams (not temporary employees) in operations, human resources, safety, IT, and procurement to identify the right talent to drive performance and results. In today’s challenging warehouse environment, a reputable managed services provider can help businesses significantly enhance their warehouse operational efficiency while freeing up time and resources that allow them to focus on what they do best.
What is a warehouse staffing agency?
Warehouse staffing agencies connect warehouse operations with local workers in a wide range of positions. Such positions might include pickers, packers, stockers, shippers, and more. Typically, these workers are tapped to provide support when warehouses need to staff up for busy seasons and special projects. As opposed to other types of integrated warehouse management partners, staffing agencies focus on temporary labor and do not offer any technology or process improvement. Another consideration is training. Typically, temporary workers are not trained to the level that warehouse management experts like Canon provide in deploying more highly trained, permanent staff.
What services do 3PLs provide?
3PLs usually own their own warehouses and invite other organizations into their facility to follow their standardized processes. Their services include receiving, storing, packing, shipping, inventory management, kitting, and light assembly. Additionally, most 3PLs offer services outside of strict warehouse management — transportation, brokerage, public warehousing etc. One important consideration is that warehousing operations often must retrofit their processes to the requirements of the 3PL, which means giving up control. Consequently, 3PLs are not specifically focused on offering a tailored solution that can be delivered onsite at their client’s warehouse location.
Assessing your warehouse inventory management
Warehouse inventory assessment includes benchmarking the desired flow and storage of inventory. From Canon’s point of view, however, an effective, comprehensive assessment goes beyond inventory considerations to comprise such key elements as: people, safety, processes, technology, and strategic growth.
Warehouse optimization
To accurately define an optimized warehouse, we must consider unique business characteristics like location, market condition, customer needs, supplier profile, and stakeholder vision. In general, an optimized warehouse has reached the highest levels of operational efficiency when it comes to driving productivity and accuracy as well as in utilizing space, labor, technology, and inventory. There are at least two areas in which many warehouses lack optimization, leading to challenges and short falls. One is delayed and inaccurate orders, often driven by unpredictable demand schedules, unacceptable levels of employee absence, and poor inventory control. The other is excessive financial burden, often caused by sub-par performance, poor management systems, and outdated processes and technology.
Considering warehouse automation
One key question addressed by an effective warehouse assessment is: “Within my operation, how do I automate as many key areas as possible?” The answer could be as simple as utilizing hand-held units to pick product and record inventory transactions or as complex as implementing AGVs (automated guided vehicles) to automate labor-intensive movements. An important point to remember is that not all warehouse operations are ready for automation, particularly those that have not yet implemented standardized processes and procedures along with best practices and a stable business model. Achieving this level of consistency is a critical prelude to successfully automating a warehouse operation. Once standardization has been achieved, automation can become a critical driver of operational success for the warehouse.
Measuring warehouse performance
Many warehouse operations do not have access to, or properly utilize, the right metrics for benchmarking and continuously monitoring performance in a way that is meaningful to their specific business. This includes using generic metrics that may not be helping the operation improve to its maximum potential. Understanding what metrics your operation needs, what metrics are available, and what technology can enable you to obtain those relevant metrics is key to effective performance management. Without this understanding, a warehouse will have no baseline for implementing short- and long-term improvements. How can a warehouse operation know if it is measuring the right things? One answer is to institute an assessment with the aid of an experienced partner like Canon that can provide valuable, objective insight based on results.
Warehouse Statistics
With ecommerce continually on the rise, additional warehouse space will be needed to meet the demand. By the end of 2021, ecommerce sales are projected to grow by 14%, intensifying the need for 330 million additional square feet of warehouse space by 2025. The ecommerce boom and the global pandemic have also brought along a new set of challenges: supply chain disruptions and labor constraints. In 2021, there are growing concerns of increased supply chain risk. According to a Logistics Management magazine survey, 39% of respondents said they had a plan to tackle that risk in 2021, compared to 52% the year prior.
Additionally, the labor gap continues to grow as warehouses grasp to retain and attract top talent. Warehousing employment has reached its highest level ever recorded in 2021, totaling nearly 1.5 million jobs. Fifty percent of warehouse operators cited labor constraints as their biggest pain point while they try to incentivize current employees to stay and reduce turnover. Warehouse operators find that they have to pay employees higher wages in order to stay competitive with other operators and major retailers who have also increased wages for employees.