Vehicle Manufacturer Taps Canon’s Expertise in Managed Workforce Services and Process Improvements
Is the traditional contingent labor model the most efficient?
A vehicle manufacturer continually investing in the future teamed with Canon Business Process Services to deliver a range of services. Over several years, these services have evolved to include implementing a more efficient system of managing employees who play a critical role in fabricating prototype vehicles. The manufacturer identified an opportunity to shift from a traditional contingent labor model to a managed workforce framework. The goal was to free up company resources currently overseeing daily staff management responsibilities so they could focus on more strategic company initiatives. The company tapped Canon’s expertise in managed workforce services to get the job done.
Outsourcing Key Functional Areas To Canon
In the initial stages of their relationship, the vehicle company engaged Canon to provide a range of shipping and receiving services. Based on Canon’s capacity to provide positive business results, the company then outsourced the management of key functional areas to Canon that include receiving, tracking, inspecting and delivering parts used to fabricate pre-prototype vehicles.
One of these key functional areas is parts control, in which Canon receives parts that are used for pre-prototype fabrication, engineering, testing and tuning. The parts are logged in, tracked and staged. Another area is parts inspection, which is designed to meet the requirement for inspecting a certain percentage of parts. Here, Canon checks the quality of these parts using tools such as micrometers and calipers. The goal is to ensure that parts received from suppliers match the design dimensions before the parts are used in test vehicles.
A third area, precision measurement, involves more in depth activities than parts inspection. Here, teams use high-tech precision measurement tools such as lasers, Faro Arms and Romer Arms that scan and measure parts to .01 micrometers—increments not detectable to the human eye.
The vehicle manufacturer is also tapping Canon’s expertise in Six-Sigma-based performance management methodologies to help drive process improvements within these functional areas. This includes parts inspection, for which Canon is currently implementing a Six Sigma® Kaizen Event. The latter is a relatively short-term, efficiency improvement project usually focused on a single or limited number of processes.
Canon’s goal is to identify potential improvements in specific procedures within parts inspection. For instance, is it possible to use technology in a way that would reduce manual data entry, which tends to be a labor intensive, error-prone process? In doing so, Canon is helping the vehicle manufacturer continually advance its operational efficiency and better prepare for the future.
In addition to performance improvement, training is also a key element of Canon’s solution. Before engaging Canon, the vehicle manufacturer trained each Canon staff member on their specific job responsibility and all other details related to employment. Now the vehicle company only trains Canon staff on their specific job. Canon handles instruction in other areas such as safety and materials handling.
Based on a successful experience partnering with Canon in the areas of parts control, inspection and precision measurement, the manufacturer’s fabrication department was confident that Canon could help improve its method of using contingent labor. One factor driving the need for contingent labor is the cyclical nature of the company’s business. Before outsourcing contingent workforce management to Canon, the fabrication department was using numerous temporary staffing agencies to fill open positions.
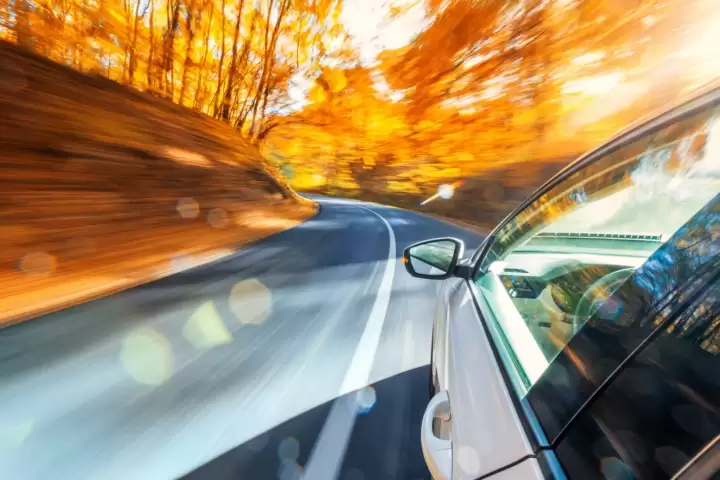
Canon Enables Significant Business Benefits
According to Canon, the Canon team has been able to achieve a number of significant business results, including the following:
- Created more consistent, higher quality staffing based on shifting from a traditional contingent labor to a managed workforce services model
- Lessened some of the challenges associated with employee training and cross-training by shifting some of these programs to Canon
- Significantly reduced costs based on transitioning to the outsourcing model
- Implemented employee and business performance management metrics
- Improved processes and procedures for areas critical to fabricating pre-prototype vehicles
- Helped identify opportunities for process improvement via Six Sigma Kaizen events
By engaging Canon, the auto company could team with a proven partner that—based on its experience in managing high quality, outsourced staff—could deliver significant improvements. These include implementing onsite management best practices, lowering costs, increasing efficiency and maintaining more consistent, higher quality, more thoroughly trained personnel who are motivated by clearly defined career opportunities. Additionally, the vehicle manufacturer would no longer have to manage many contracts with different agencies and could also rely on Canon to implement employee performance metrics that help drive continuous improvement.