Canon Helps Top Children's Hospital's Supplies Distribution Process
Canon Develops Optimized Plan For Managing Medical Supplies
Before we worked with one of the nation’s top children’s hospitals, it had a plan for managing and distributing medical supplies. Working with an outsourcing vendor, the hospital strategized around keeping its nurses well supplied with the equipment they needed. But when the hospital grew over a five-year span—nearly tripling its staff—the original plan didn’t grow proportionally. That’s when supplies went from managed to mismanaged.
Many items were understocked—much to the chagrin of the nurses who used them—while other items were drastically overstocked. Thousands of dollars’ worth of medical supplies regularly exceeded their expiration dates. Again and again the hospital paid for more supplies than it could use. The issues spilled over to employment. Personnel turnover and absenteeism, particularly on holidays and weekends, were at an alarming level. The hospital was often understaffed and undersupplied. “After concluding that our outsourcing partner was not adequately responding to the challenges we were facing with efficiently storing and distributing supplies, as well as other related issues, we decided to take action,” said a hospital executive. The hospital addressed the situation by inviting our team at Canon to deliver a diagnosis and develop a future-proof, scalable plan.
People Come First
We began the partnership by assessing and fixing the distribution system’s two main issues: the people and the process. People came first. We recruited and hired a staff that was familiar with the hospital’s existing materials distribution system, then trained them with a focus on customer service, accountability, and teamwork. With this staff in place, we were very confident that any process would be executed smoothly each day.
Then came the process itself. We brought in the Canon management team and our process consultants, who staged Lean Six Sigma® Kaizen Events to rewire workflows for maximum efficiency. The process team minimized the time it takes to stock, pick, inventory, and reorder medical supplies. The team also reorganized where supplies are stored so items can be found quickly and accurately—important factors, for instance, when a specific item is needed for surgery.
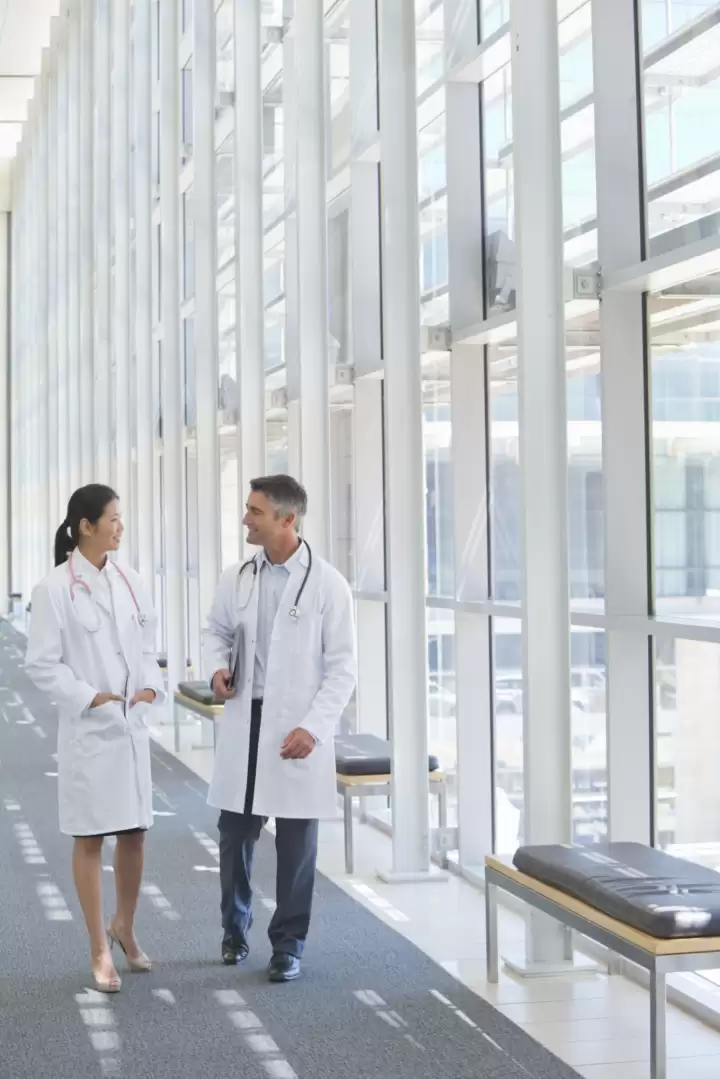
Making A Difference
The process team also reviewed workflows for 48 endoscopic mechanical items and found ways to reduce inventory levels for over 40 of them—freeing up storage space and cutting costs by over $40,000. “As a last, critical step, Canon helped mend our distribution team’s relationship with the hospital’s ‘customers,’ our nurses,” added the hospital executive. “Canon began conducting daily meetings with the nursing staff to set objectives and relay results. Relations began improving almost immediately.”
To date, this combination of increased communication, decreased waste, and improved workflows has helped the hospital run smoothly again. One senior member of the hospital’s staff called our transition a “nonevent”—proof that the hospital can once again focus on treating its patients, not its own processes. Learn more about Canon's Medical Supplies Distribution and Logistics Management service.